The art of violinmaking
"The Art of Violin Making"
That's the name of the textbook for German violin makers. It was written by the Berlin master violinmaker Otto Möckel.
This specialist book provides the basic knowledge for the manufacture of violins.
The profession of violin maker is very diverse and includes new construction, acoustics, repair, care and maintenance of stringed instruments, such as: the violin (violin), viola (viola), cello (violoncello) and the double bass. In addition to the modern string instruments of the violin family, a few specialized violin makers also build historical string instruments of the gamba family such as viola da gamba, fiddle, quinton, rebec, baryton, viola d'amore....
The bows required to play the stringed instruments are serviced and cared for by violin makers, for example newly covered with horse hair.
The string bows are made by the guild of bowmakers.
Training to become a violinmaker in Germany takes three years. It ends with the journeyman's examination at the Chamber of Crafts.
Prerequisite for learning the profession of violinmaker is:
A great skill and care in the millimeter-precise processing of the wood with the hand tools, such as. Chisels, carvers, planes and
a good ear for tuning the wooden panels and for tuning and checking the sound and functionality of an instrument.
a sense of art and aesthetics when designing the instrument and varnishing the Instruments
In our workshop UEBEL-since 1725 we would be happy to build your individual violin, viola and cello for you or optimize your existing violin individually to suit your wishes.
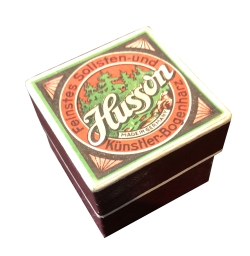
.
Making new instruments
Continuing the proven family tradition, Frauke Uebel manufactures each of her high-quality instruments individually by hand.
Many different work steps are carried out when building a stringed instrument. In the workshop of Geigenbau UEBEL - since 1725 only the best, very long-seasoned and air-dried tonewood is used, most of which still comes from the wood store of the ancestors.
Great craftsmanship and attention to every detail, no matter how small, is necessary when building a new stringed instrument, as is the exact observance of all scales. All of this, as well as the choice of tonewood, the design of the arches and the careful matching of thickness of top and back contribute to the overall sound, the easy playability and the problem-free handling of a new violin.
Thus every instrument from UEBEL - since 1725 becomes an individual, sounding work of art.
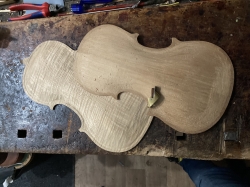
Tonewood
For the new construction of the instruments, UEBEL - since 1725 only uses air-dried tonewood that has been seasoned for at least 30 years. For the most part, the workshop can still fall back on the tonewood of the ancestors. It was common for the wood store to be well stocked for the next generation.
Spruce (Picea abies) is chosen for the soundboard of a violin because the wood has grown regularly and consists of annual rings of equal width. An ideal tonewood trunk, from which the top is made, grows like a straight circular cylinder and should be free of knots for at least 5 meters. The spruce tonewood with these requirements comes from mountain forests, often from the Kapaten but also from Switzerland, Italy, Germany, Austria and France.
Traditionally, sycamore maple (Acer pseudoplatanus L.) is used for the back, sides and scroll of violins. The flames running across the direction of growth of this hardwood are particularly beautiful. This grain is created by a wavy growth.
The Bosnian maple is preferably used in violin making, Antonio Stradivari already chose this for his world-famous violins.
Tools for violinmaking
Here we would like to introduce you to some typical, traditional tools, some of which were only invented for violin making